Hydrostatics is the science that studies the behavior of liquids at rest. The pressure arising from the accelerations in these fluids is called hydrostatic pressure. It is a test to determine material strength and life by measuring the deformation caused by hydrastatic internal pressure in plastic or thermoplastic pipes such as Polypropylene (PP), Polyethylene (PE), Polyvinyl chloride (PVC) under constant temperature and pressure. Values such as temperature, pressure etc. and other conditions are determined by some standards such as ISO 1167, BS EN 921 and ASTM D1598.
Why is Hydrostatic Internal Pressure Test Done?
Today, the transfer of many important resources is provided with the help of pipes. The durability of the pipes is important in terms of human life, waste of resources and prevention of environmental pollution. For this reason, the pipes produced must comply with the standards determined according to the area in which they will be used. In order for PE, PP, PVC and PE RT pipes to be used safely, the working conditions and service life at certain temperature and pressure values should be known according to the area in which they will be used. In order to determine these conditions, the pipes must pass the hydrostatic internal pressure test. By comparing the obtained values with the standards, it is determined whether they are suitable for use or not.
Standards
ISO 1167, BS EN 921, ASTM D1598 are standards that explain in detail the rules that must be followed in a hydrostatic internal pressure test and the conditions that the test environment and test elements must be. In them, the shapes of the fasteners and the methods of connecting the elements are determined. Here, It is stated that the dimensioning of the sample to be tested should comply with ASTM D2122 and ASTM D3567 standards.
According to BS EN 921 and D1598 standards, the sensitivity of the conditioning and pressure devices to be used in the test should be at the level of ± 2%. The temperature of the environment, fasteners and test liquid should be 23 Cᵒ. According to the D2122 standard, pipes 150 mm (6 in.) in diameter and smaller must have a length of at least five times the outer diameter of the pipe. For pipes with a larger diameter, this value should be at least three times the outer diameter.
Test Equipments
The test system consists of one upper and lower closing caps, clamps for fixing these caps, mounting and sealing elements, conditioner, liquid tank and pressure device.
How to Do the Test?
The sample selected in accordance with the standards is closed at both ends with end caps. It is filled with liquid brought to the desired temperature with the help of a conditioner until there is no air in it. Then, the sample is made ready for testing by being completely immersed in the conditioned medium by being supported so that it does not warp due to weight. According to the EN 921 standard, samples with a wall thickness of less than 3 mm should be subjected to conditioning for 1 hour, those with 3-8 mm for 3 hours, those with 8-16 mm for 6 hours, and those with a greater than 16 mm for 16 hours.
By adjusting the pressure level with a pressure machine, it is applied to the sample that is ready, and the test is started by starting the counter at the same time. The variation of the deformation in the sample with respect to time is recorded. Pressure will be applied to specimens is calculated by the equation given:
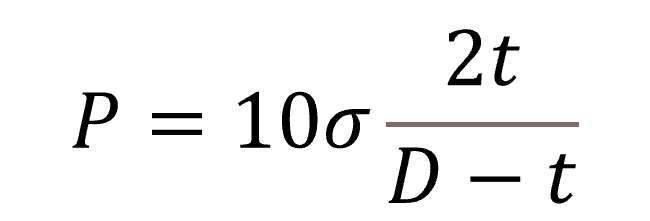
P = Pressure (bar) σ = Hoop Stress (MPa) D = Pipe Outer Diameter (mm) t = Wall Thickness (mm)
Hup stress is the tensile stress induced along the entire circumference of the pipe due to the applied pressure.
If a puncture or leakage occurs on the sample while the test is in progress, the test is stopped and the type of deformation is recorded as brittle or ductile. According to EN 921, if the error occurs closer to the closing caps than 0.1 times the length of the pipe, the test is canceled and the test is repeated with a new sample.
In case of an explosion during the test, precautions should be taken and if a gas is used instead of liquid, the potential energy storage capabilities of gases should not be ignored. The equipment and environment to be tested must be free of oil and dirt.
Evulation of Test Results
If the pipes exposed to pressure during the test do not burst within 100 hours at 20°C, and 165 hours at 80°C [1], which is the time determined by the standards, or if the graphs do not show values above the determined deformation, it is decided that the pipe is suitable for use.
Usage Areas
Plastic and thermoplastic pipes have found wide usage area due to reasons such as easy workmanship, low cost, low maintenance requirement and not being exposed to corrosion. It is widely used in network systems because it can transport waste water as well as resources such as natural gas, clean water and geothermal water. In addition to these, it continues to be used in agricultural irrigation. Hydrostatic pressure test is involved in the safe use of plastic pipes in these sectors.
References:
[1] – https://topuzplastik.com.tr/testler/